PRINCIPLES OF YARN CLEARING /YARN CLEARING IN WINDING / ASSESSMENTS OF CLEARER PERFORMANCE
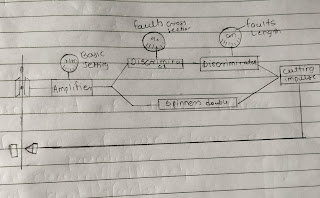
Objective of yarn clearing - Objective of yarn clearing is to remove objectionable faults from the yarn / supply package Principles of measurement of yarn faults/Yarn diameter Two principles are used in morden winders for identification of yarn faults 1. Capacitance principle 2.Optical principle 1.Capacitance principle - Working Principle- : When yarn pass through two capacitor parallel plate the electrical signal changes / produce which is proportional to change in mass per unit length. Capacitance (C) = εA /d C= charge/Voltage Working -: In the capacitor electronic yarn clear device is measurement of yarn mass per given test length Any change in mass of yarn then the set value to makes corresponding change in a capacitance. The signal is send to the amplifier. The amplifier amplifies the signal and compared with previously set value in the discriminator . If the limit is goes above the set v